How MMC Materials digitized 12,000 inspections
MMC Materials, a leading building materials company, used Mapistry to manage environmental compliance across 90 locations and digitized more than 12,000 inspections.
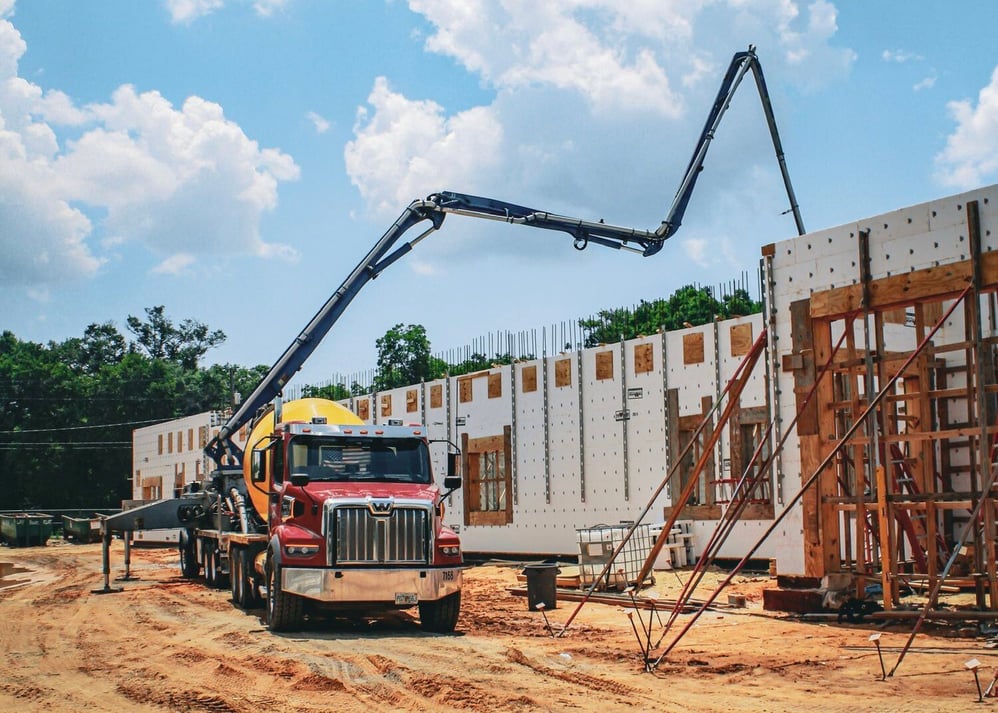
MMC Materials, a leading building materials company specializing in ready-mix concrete, faced significant challenges in managing environmental compliance across its 90 locations.
Relying on paper-based inspections led to inefficiencies, compliance risks, and a lack of standardization. MMC Materials adopted Mapistry, which streamlined inspections, increased accountability, and improved compliance management.
The challenge: 12,000 paper-based inspections were burning up company resources
MMC Materials dealt with an overwhelming volume of paper-based inspections—over 12,000 per week across 90 concrete facilities.
The process was time-consuming and inconsistent, with managers often struggling to track inspections and corrective actions. This resulted in:
- Operations "pencil-whipping" inspections to get them off their plate
- Difficulty in verifying the completion and accuracy of inspections
- Managers spent more time tracking paperwork than improving plant operations
"The effort to track inspections and corrective actions impaired site managers’ ability to focus on other areas of plant improvement." – Gary Scott, Area Manager
Not changing their process wasn’t an option anymore
Without a better system, MMC Materials risked:
- Getting fined for incomplete inspections, with potential six-figure EPA penalties.
- Wasting six-figure employees on paperwork, with managers being stuck in compliance instead of improving processes in the plant.
Why MMC Materials chose Mapistry
MMC Materials wanted a platform that could:
- Digitize the inspection process and give time back to operations.
- Provide real-time compliance data across all facilities.
- Increase accountability and streamline reporting processes.
What made Mapistry stand out for MMC
- A user-friendly mobile app that operations wanted to use.
- Offline inspections for remote locations without internet access.
- A centralized dashboard for monitoring compliance across multiple sites.
"The offline access helps too because some of our plants are remote. They can still take their pictures and make their notes. And when they connect to Wi-Fi, it uploads everything." – Sonya Price, Regional EHS Manager
The transformation: Easy inspections on the Mapistry App
and a reliable compliance system
MMC Materials integrated Mapistry for:
- SPCC, stormwater, and waste inspections
- Environmental, OSHA, and MSHA compliance monitoring
- Document management for permits and training logs
Even inspectors were impressed with the improved system
After implementing Mapistry, MMC Materials saw immediate improvements:
- Thorough inspections getting completed on time.
- Operations getting time back to improve processes in the plan.
- Improved accountability, with managers taking greater ownership of compliance.
"I’ve had three inspections since implementing Mapistry. All inspectors were impressed with our use of Mapistry." – Sonya Price, Regional EHS Manager
Would MMC Materials recommend Mapistry? Yes.
MMC Materials highly recommends Mapistry for its ease of use and compliance benefits.
"Mapistry has helped motivate and give accountability for compliance across our facilities. Managers can now take ownership in their sites." – Gary Scott, Area Manager
Drowning in paperwork? MMC Materials was too.
With 12,000 inspections per week across 90 locations, their compliance process was a nightmare—until they switched to Mapistry. Now, inspections are streamlined, accountability is up, and operations have time to focus on what matters.
Stop wasting time on paperwork. Let’s talk about how Mapistry can help your team.